Finished Attics: A Lower-Carbon and Lower-Cost Retrofit Approach
September 2021by Brendan Kavanagh
When Boston area homeowners need more space, often the first place they look is up. The problem is that many attic conversions, even those done relatively recently, have little to no air sealing, poorly installed insulation, and ineffective roof venting. The result is finished space that can be hard to heat, cool, and keep dry.
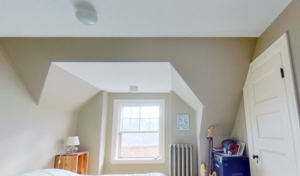
Byggmeister’s approach to these spaces has been to remove the finishes from the sloped areas, insulate the underside of the roof with closed-cell spray foam, and install new finishes. This method has yielded great results but is disruptive, expensive, and carbon-intensive. A lower-cost and lower-carbon alternative would be to leave the finishes intact and to switch from spray foam to blown-in cellulose. When we use an air-permeable insulation such as cellulose, the building code requires a vent space between the insulation and the roof sheathing. Retrofitting this space generally requires removing finishes – exactly what we’re hoping to avoid. Wouldn’t it be nice if we could forego the ventilation space and just dense-pack the rafter cavity? Other contractors do this, some routinely. But contractors (including us) do a lot of things that don’t always stand the test of time.
As luck would have it, the team at Building Science Corporation(BSC) ran a study on the unvented roof approach and recently published the results: Monitoring of Unvented Roofs with Fibrous Insulation, Diffusion vents, and Interior Vapor Control in a Cold Climate. In this study, they observed that dense-packed cellulose in unvented roof assemblies sometimes caused the roof sheathing to become wet enough for long enough to lead to mold growth; however, these conditions occurred primarily at the highest points of the roof near the ridge. In the section titled “Further Work” they suggest that if an open attic with adequate venting is maintained above unvented slopes, the additional drying potential might keep the area near the ridge dry enough to avoid the conditions they observed in their study. They go on to cite many others who state that this “short slope” approach has been used by weatherization contractors in cold climates since the early 90’s without reported callback issues or observed moisture damage during inspections.
We decided to try the “short slope” approach on a few projects and install some moisture monitoring equipment both to reassure our clients, ourselves, and skeptical building officials, and also to help create a data set in support of this method.
The first project we did has several features that make it an interesting test case. The third floor was completely finished with a shed dormer across most of the backside. Th south-facing back roof has a 4:12 pitch and solar panels covering most of it. The rest of the roof is closer to a 9:12 pitch and faces mostly north except for two short sections. It has relatively new asphalt shingles over board sheathing with no existing venting. All the slopes were finished on the inside, but the view through a small access panel indicated that the only existing insulation was a 1” fiberglass batt on top of the ceiling.
Our prior approach — removing all the ceiling finishes, insulating with low GWP closed cell spray foam, and installing new finishes – would have generated approximately 3,000 kilograms of CO2e and would have cost a lot. We estimate that our new approach — leaving the finishes in place and switching to cellulose – reduced the embodied carbon impact to around -1,000 kg CO2e (yes, a negative carbon impact) and cut the cost by almost 50%.
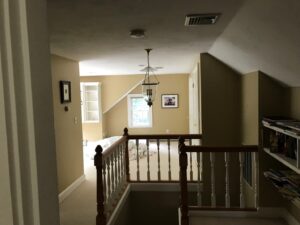
With this approach, it's critically important to achieve good cellulose density because the resilience of the assembly relies on minimal airflow through the insulation and full contact with the roof sheathing. The ideal target is around 4 lbs/ft3. To monitor density we asked our cellulose installer to pack the sloped areas first and count how many bags of cellulose they used. We estimated the volume of the cavity space we were insulating and, using the pounds of cellulose per bag, calculated an installed density of around 3.8 lbs/ft3, not too bad.
We installed just over a dozen monitoring devices to record temperature, humidity, and the percent moisture content of the roof sheathing in a variety of locations. The yellow comment boxes show where in the assembly the monitors were located. The installation was completed towards the end of 2020. So far, the data show that only the roof sheathing above the loose blown cellulose near the new ridge vent is reaching a moisture content above 15%. The monitors in that area hovered around 20% between January and March. They spiked a couple times to just over 25% but always dropped back towards 20% in a day or two. In March all monitors dropped below 15% and most have been in single digits ever since. These initial results seem very consistent with the BSC research indicating that moisture accumulates near the ridge in the colder months but dries out quickly in the spring.
We are now completing our third project using this strategy and are due to start a fourth this autumn. We are continuing to install monitors in each project, principally in those areas that might be higher risk, such as dormers with no venting of their own and little to no connection to the main vented attic space. We’ve also installed a few monitors in dense packed slopes between soffits and vertical dormer walls to see if lack of connection to the attic above could lead to moisture accumulation there.
A big concern of ours going into this was push back from building inspectors based on the lack of code compliant venting. On our first two projects we provided an architect-stamped letter when we applied for the building permit, requesting approval of the approach under MA 780 CMR:104.11 Alternative Materials, Design, and Methods of Construction. On our third project we didn’t provide a stamped letter at permit application but are prepared to provide one if the inspectors aren’t comfortable with our explanation and monitoring strategy.
We are hopeful that the data from our monitoring will show that these assemblies are staying dry enough for us to continue choosing cellulose over spray foam in finished attic retrofits. Once we have a few more seasons of data from our handful of projects we plan to share the results with our colleagues and see where that takes us.
This is the third in a series of blog posts on reducing embodied carbon in residential retrofits. The first post is Rethinking Our Approach to Insulation. The second is Two Carbon Smart Ideas in the Attic.